- Real-Time Inventory Tracking
- Automated Reordering and Stock Alerts
- Multi-Channel Inventory Management
- Advanced Reporting and Analytics
- Integration with Other Business Tools
- Scalability and Customization
- User-Friendly Interface and Mobile Accessibility
- Customer Support and Training Resources
- Robust Security and Compliance Features
- Cost-Effectiveness and ROI
- Conclusion
- Frequently Asked Questions (FAQs)
Table of Contents
Key Features of the Best Inventory Management Systems
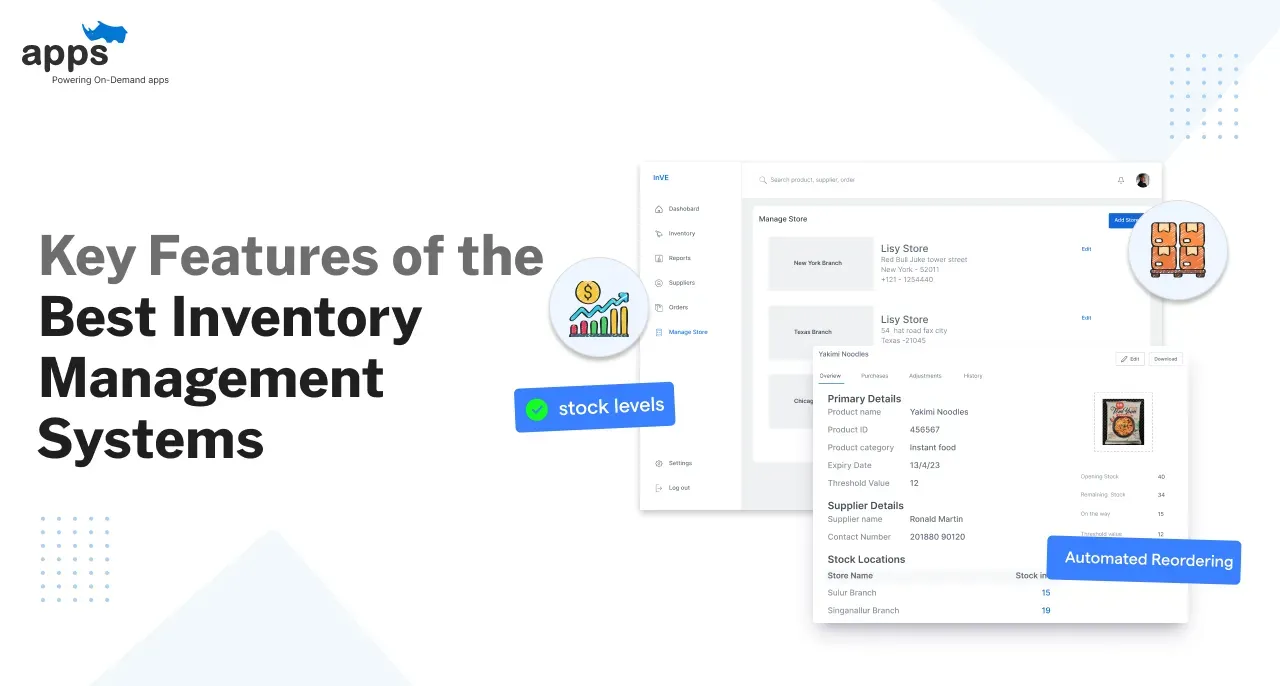
Inventory management is a critical aspect of running a successful business, yet many companies struggle with challenges like overstocking, stockouts, inefficiencies, and lost revenue.
These issues not only drain resources but also hinder growth and customer satisfaction.
The good news?
The right inventory management system can transform your operations, save time, and boost profitability.
In this blog, we’ll explore the key features to look for in a top-tier inventory management system, helping you make an informed decision that addresses your specific pain points.
Whether you’re a small business owner or managing a large enterprise, these insights will guide you toward the best inventory management software for your needs.
Real-Time Inventory Tracking
In today’s fast-paced business environment, staying on top of inventory levels is no longer a luxury—it’s a necessity.
Manual tracking methods are outdated, error-prone, and inefficient, leaving businesses vulnerable to stock discrepancies, lost sales, and operational inefficiencies.
Enter real-time inventory tracking, a most engaging feature of modern inventory management systems.
In this blog, we’ll explore how real-time inventory tracking works, the pain points it addresses, and why it’s a must-have for businesses looking to streamline operations with Custom Inventory Management Software and help in increasing profitability.
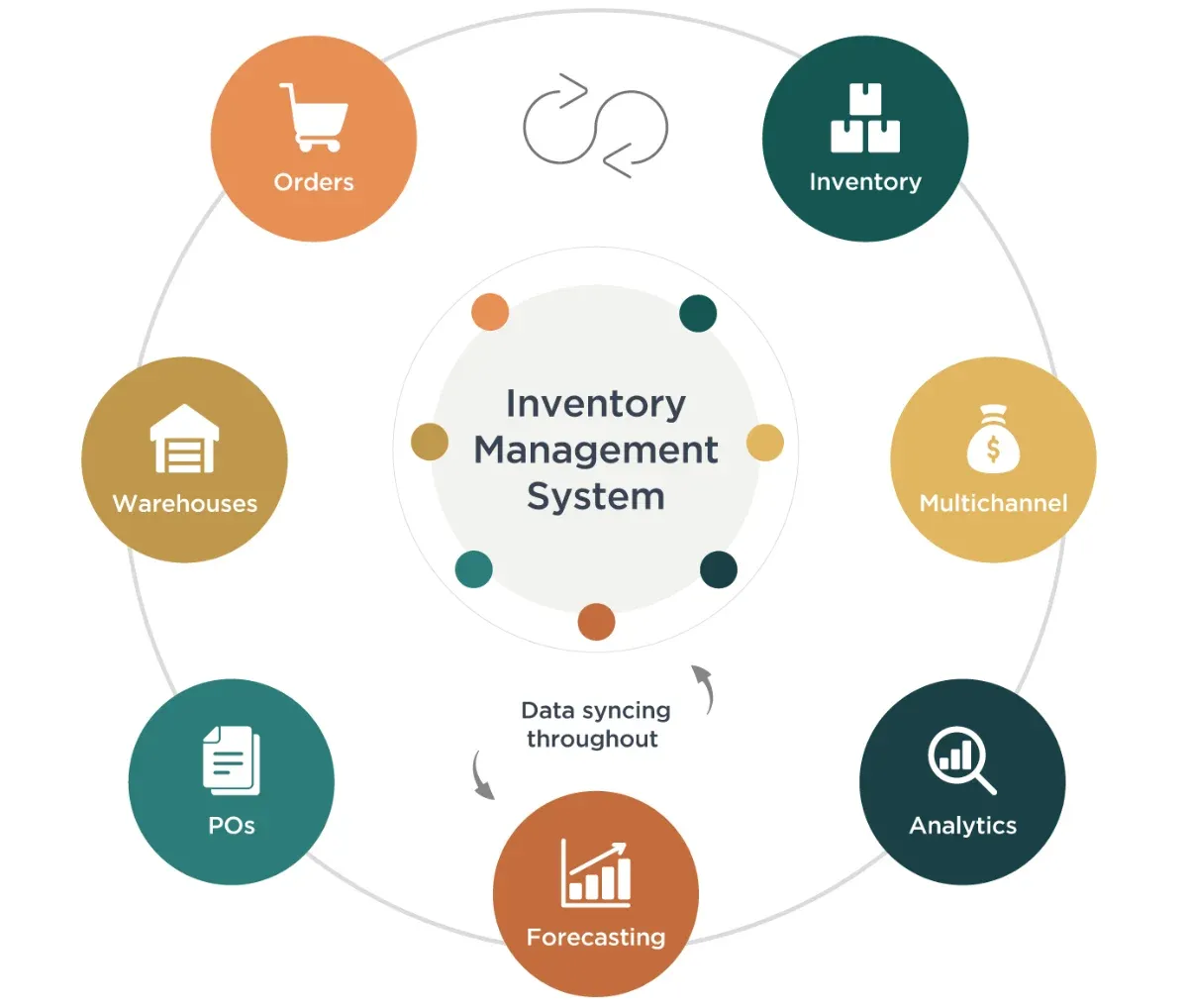
Pain Point Addressed: Eliminating Manual Tracking Errors
Manual inventory tracking is a tedious and error-prone process. Miscounts, misplaced items, and outdated records can lead to:
- Stockouts: Running out of popular items, resulting in lost sales and unhappy customers.
- Overstocking: Tying up capital in excess inventory that may not sell.
- Operational Inefficiencies: Wasting time and resources on manual counts and reconciliations.
Real-time inventory tracking eliminates these issues by providing accurate, up-to-date stock levels at all times. This ensures businesses can meet customer demand, optimize stock levels, and reduce unnecessary costs.
Example: A retail business reduced stock discrepancies by 30% after implementing a real-time tracking system, saving thousands in lost revenue.
Automated Reordering and Stock Alerts
Running a business is no small feat, especially when it comes to managing inventory. Stockouts can lead to lost sales, while overstocking ties up valuable capital.
Enter automated reordering and stock alerts—feature of modern inventory management systems.
In this blog, we’ll explore how this custom solution works, the pain points it addresses, and why it’s a must-have for businesses looking to optimize their operations.
Pain Point Addressed: Preventing Stock outs and Overstocking
For business owners, inventory management is a constant balancing act. Too little stock means lost revenue, while too much stock leads to wasted resources. This is where automated reordering shines.
The Problem:
- Stockouts: Customers can’t purchase what they want, leading to frustration and lost sales.
- Overstocking: Excess inventory ties up cash and increases storage costs.
The Solution:
Automated reordering ensures that inventory levels are always optimized. By setting predefined thresholds, the system takes care of the rest, ensuring you have just the right amount of stock at all times.
Key Takeaway: An inventory management system with automated reordering is the ultimate solution for businesses looking to eliminate stockouts and overstocking.
Real-World Example
An e-commerce store implemented an inventory management system with automated reordering and saw a 25% improvement in order fulfillment rates.
By setting custom reorder points and integrating with their suppliers, they were able to reduce stockouts and improve customer satisfaction.
Multi-Channel Inventory Management
In today’s fast-paced retail environment, businesses often sell across multiple channels—online stores, marketplaces like Amazon and eBay, and physical stores.
While this multi-channel approach expands your reach, it also introduces complexities in managing inventory.
An inventory management system designed for multi-channel operations ensures that your stock levels are consistent across all platforms, preventing overselling and stockouts.
For business owners, this means happier customers, fewer logistical headaches, and more time to focus on growth.
Pain Point Addressed
One of the biggest challenges of multi-channel selling is overselling. Imagine a customer purchasing a product on your website, only to find out it’s out of stock because the same item was sold on Amazon.
This not only leads to disappointed customers but also damages your brand reputation.
A robust inventory management system solves this by syncing stock levels in real-time across all your sales channels.
This ensures that your inventory is always accurate, no matter where the sale happens.
Example: A multi-channel retailer struggling with inconsistent stock levels implemented a real-time syncing inventory management system.
Within months, they reduced overselling by 90% and increased sales by 20%—simply by ensuring products were always available when customers wanted to buy.
Advanced Reporting and Analytics
In the world of inventory management, data is king. An inventory management system with advanced reporting and analytics empowers businesses to make data-driven decisions.
By identifying trends, predicting demand, and spotting slow-moving items, you can optimize your inventory and maximize profitability.
For business owners, this means turning raw data into actionable insights that drive growth.
Pain Point Addressed
Many businesses struggle with excess stock or stockouts because they lack visibility into their inventory performance.
Without accurate data, it’s impossible to know which products are selling well, which are gathering dust, and when to reorder.
The best system for inventory management addresses this by providing detailed reports and predictive analytics. This helps you:
- Identify trends and seasonal demand patterns.
- Forecast future inventory needs with precision.
- Reduce carrying costs by optimizing stock levels.
Example: A wholesale business used predictive analytics to optimize their inventory turnover. By identifying slow-moving items early, they reduced excess stock by 30% and improved cash flow significantly.
Integration with Other Business Tools
In the digital age, businesses rely on a variety of tools to manage operations, from accounting software to CRM and ERP systems.
However, without seamless integration, these tools can create data silos, leading to inefficiencies and errors.
A robust inventory management system that integrates with your existing tools can streamline workflows, reduce manual effort, and provide a unified view of your operations.
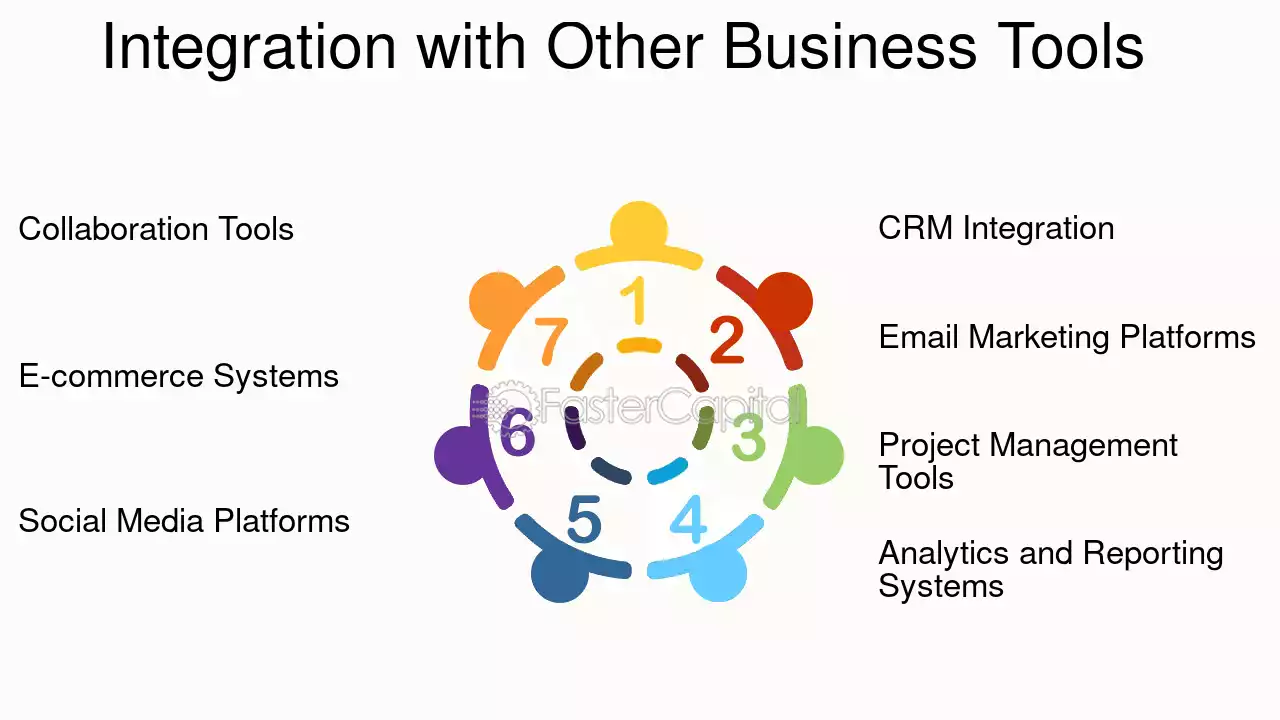
Pain Point Addressed
Many businesses struggle with disconnected systems that require manual data entry, leading to errors, wasted time, and missed opportunities.
An integrated inventory management system ensures that data flows seamlessly between platforms, eliminating silos and improving accuracy.
Example: A manufacturing company integrated its inventory management system with QuickBooks and Salesforce. This integration reduced manual data entry by 50%, saving countless hours and minimizing errors.
Scalability and Customization
As your business grows, so do your inventory management needs. A system that works for a small startup may not suffice for a larger enterprise.
Scalability and customization are crucial for ensuring your inventory management system can adapt to your evolving requirements.
Pain Point Addressed
Many businesses outgrow their initial systems, leading to costly migrations or workarounds.
A scalable inventory management system grows with your business, accommodating higher inventory volumes, additional locations, and new product lines.
Example: A startup in the e-commerce space chose a scalable inventory management system that supported its growth from a single warehouse to multiple locations. The company avoided the hassle of switching systems and maintained seamless operations throughout its expansion.
Due to technical issues, the search service is temporarily unavailable.)
User-Friendly Interface and Mobile Accessibility
In today’s fast-paced business environment, an inventory management system must be easy to use and accessible from anywhere.
A user-friendly interface and mobile accessibility are no longer optional—they are essential for businesses looking to streamline operations and stay competitive.
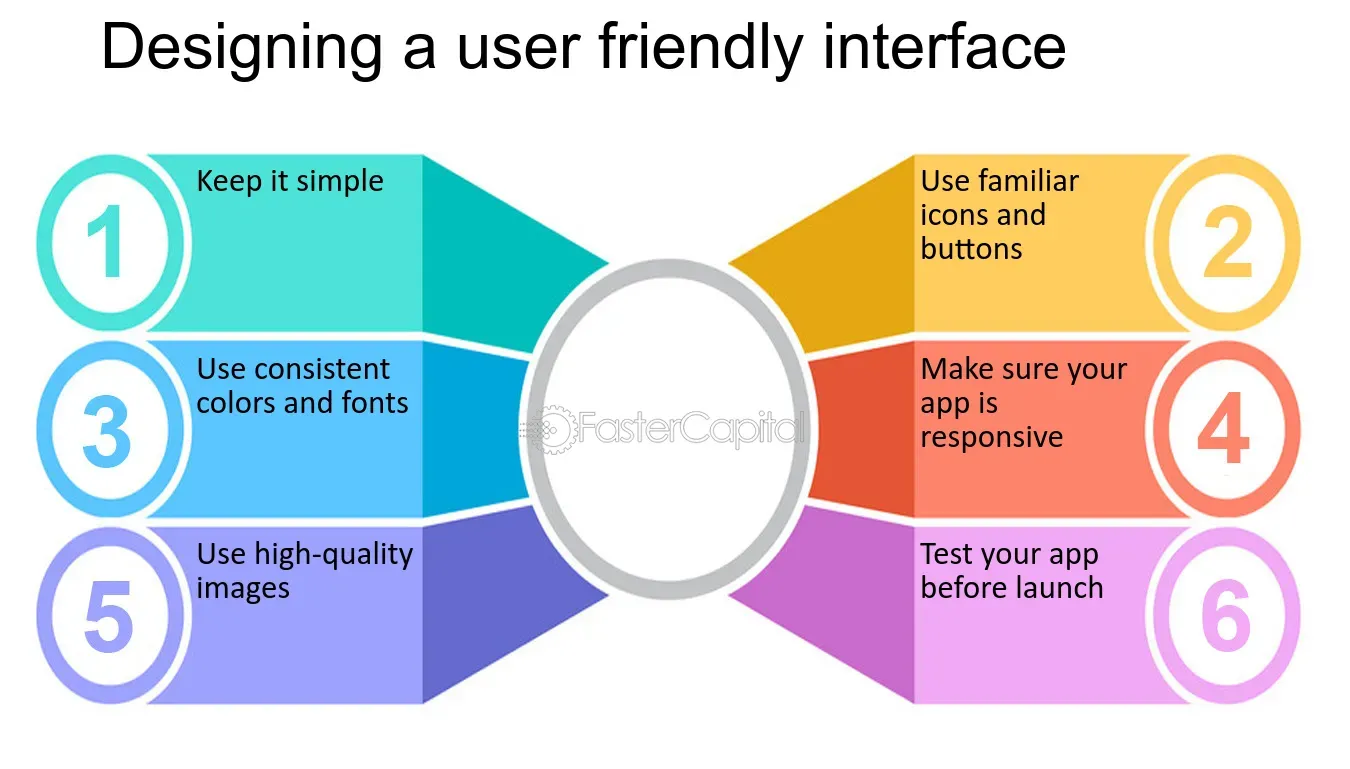
Pain Point Addressed
For many business owners, complex systems require extensive training, eating into valuable time and resources.
Additionally, the inability to monitor inventory on the go can lead to inefficiencies and missed opportunities.
A system with a user-friendly interface and mobile accessibility reduces training time and allows managers to oversee inventory operations from anywhere, ensuring seamless business continuity.
Example: A small business owner was able to improve efficiency by using a mobile app to manage inventory while on the go.
This allowed them to quickly restock popular items, reducing stockouts and increasing customer satisfaction.
Customer Support and Training Resources
When implementing a new inventory management system, reliable customer support and training resources are non-negotiable.
These elements ensure a smooth transition, minimize downtime, and help your team maximize the system’s potential.
Pain Point Addressed
Many businesses struggle with system implementation and ongoing optimization. Without proper support, even the best tools can fall short of expectations.
Key Differentiators
The best inventory management software offers
- 24/7 customer support to resolve issues quickly.
- Onboarding assistance to help your team get up to speed.
- A comprehensive knowledge base for self-service troubleshooting.
Example: A retail business faced a critical system error during peak season. Thanks to 24/7 support, the issue was resolved within hours, preventing significant revenue loss.
Robust Security and Compliance Features
Data security and compliance are critical for any business, especially when dealing with sensitive inventory and customer information.
A reliable inventory management system must prioritize robust security measures and adhere to industry standards to protect your business from risks.
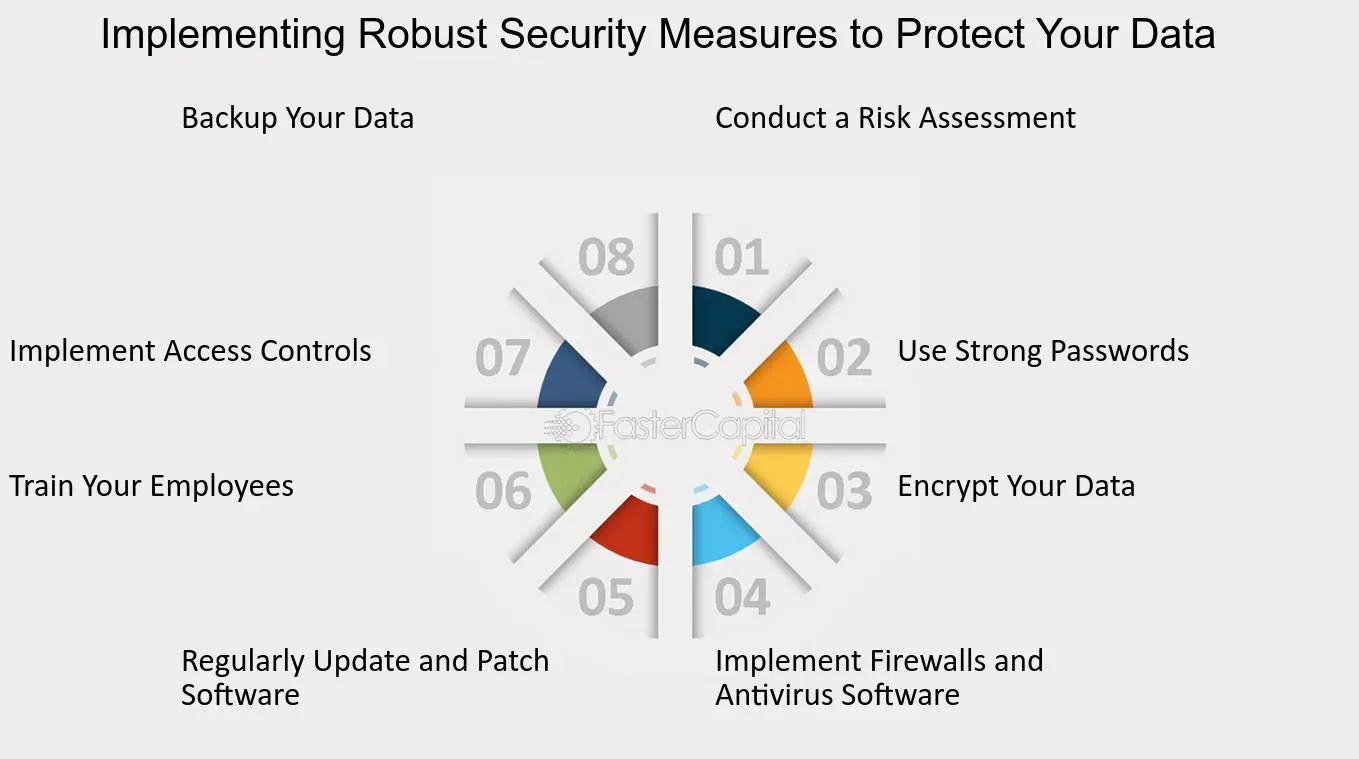
Pain Point Addressed
Businesses often struggle to safeguard sensitive data and ensure compliance with regulations like GDPR, HIPAA, or industry-specific standards.
A system with strong security features protects your business data and ensures you meet regulatory requirements, giving you peace of mind and avoiding costly penalties.
Example: A healthcare supplier successfully ensured compliance with HIPAA regulations by using an inventory management system with advanced security features.
This not only protected patient data but also streamlined their operations, saving time and resources.
Cost-Effectiveness and ROI
Investing in an inventory management system shouldn’t break the bank. The right solution delivers value for money, ensuring you only pay for the features you need.
Pain Point Addressed
Many businesses overspend on systems with unnecessary features or hidden costs, leading to wasted resources.
Key Differentiators
The best system for inventory management stands out by offering:
- Transparent pricing with no hidden fees.
- Free trials to test the system before committing.
- Measurable ROI through cost savings and efficiency improvements.
Example: A manufacturing company saved $10,000 annually by switching to a cost-effective solution that eliminated redundant features and streamlined operations.
Conclusion
Choosing the right Custom inventory management system is a strategic decision that can transform your business.
From robust customer support to cost-effective solutions, the best inventory management software addresses common pain points and delivers tangible results.
By investing in the best system for inventory management, you can:
- Streamline operations and reduce errors.
- Save time and money with optimized processes.
- Scale your business with confidence.
Why not take it a step further? With Joget, you can build a customized inventory management system tailored to your unique business needs.
And if you’re looking for expert implementation and support, AppsRhino provides end-to-end Joget solutions to ensure seamless integration and maximum efficiency.
Take the next step today! Explore how Joget and AppsRhino can help you build the perfect inventory management solution. Book a demo, start a free trial, or contact their team to see how they can transform your business operations.
Frequently Asked Questions (FAQs)
What are the must-have features in an inventory management system?
The best systems include real-time tracking, barcode/QR scanning, automated reordering, demand forecasting, multi-channel sync, and detailed reporting.
How does real-time inventory tracking benefit my business?
It prevents stockouts and overstocking, improves order accuracy, and enhances supply chain efficiency by providing live updates on stock levels.
Can inventory management software integrate with other business tools?
Yes, top systems integrate with eCommerce platforms (Shopify, Amazon), accounting software (QuickBooks), and ERP systems for seamless operations.
Is cloud-based inventory management better than on-premise solutions?
Cloud-based systems offer remote access, automatic updates, and scalability, while on-premise solutions provide more control but require higher maintenance.
How does automation in inventory management save time and reduce errors?
Automation handles repetitive tasks like stock updates, purchase orders, and low-stock alerts, minimizing manual errors and improving efficiency.
Table of Contents
- Real-Time Inventory Tracking
- Automated Reordering and Stock Alerts
- Multi-Channel Inventory Management
- Advanced Reporting and Analytics
- Integration with Other Business Tools
- Scalability and Customization
- User-Friendly Interface and Mobile Accessibility
- Customer Support and Training Resources
- Robust Security and Compliance Features
- Cost-Effectiveness and ROI
- Conclusion
- Frequently Asked Questions (FAQs)