- Key Components of Pharmacy Automation Systems
- Types of Pharmacy Automation (By Functional Stage)
- Pharmacy Automation System Workflow: Step-by-Step Operations
- Benefits of Pharmacy Automation Systems
- Challenges and Limitations
- Real-World Use Cases of Pharmacy Automation
- Technologies in Pharmacy Automation Systems
- Conclusion
- Frequently Asked Questions (FAQs)
Table of Contents
How does Pharmacy Automation Systems work?
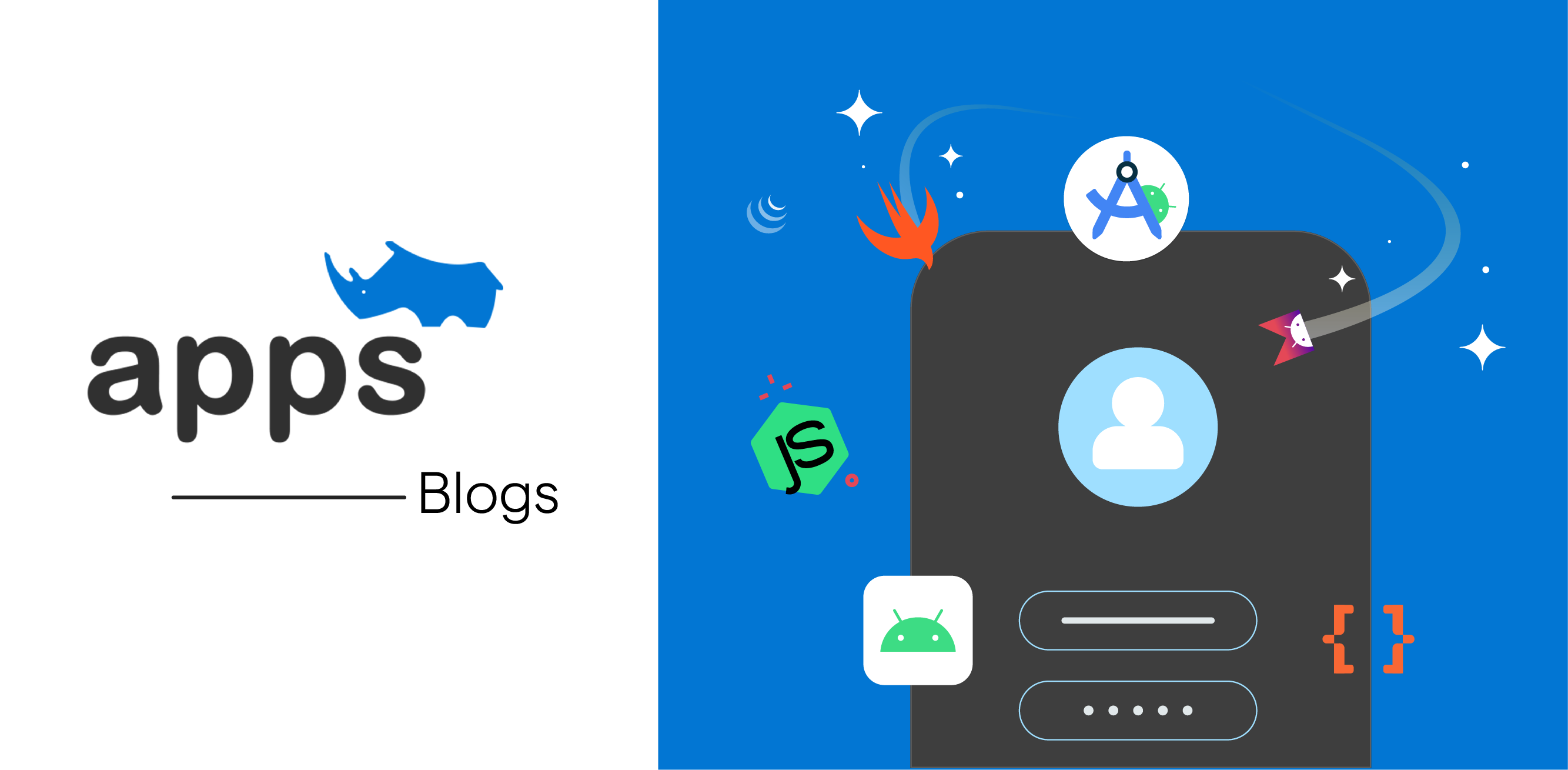
Pharmacies today face two major challenges: rising prescription volumes and ongoing workforce shortages. Manual processes can no longer keep up without compromising speed, accuracy, or safety.
Pharmacy automation systems offer a scalable solution by integrating hardware and software to streamline operations. With advancements in AI, robotics, and IoT, these systems now handle everything from inventory and dispensing to labeling and packaging — all with minimal human intervention.
By reducing repetitive tasks and enabling real-time oversight, pharmacy automation systems helps improve patient outcomes, cut wait times, and boost operational efficiency. It’s not just about machines — it’s about modernizing pharmacy care.
Key Components of Pharmacy Automation Systems
Modern pharmacy automation systems rely on seamlessly integrating software and hardware to streamline medication workflows.
Each component plays a distinct role, but their true power lies in how they work together to minimize errors, cut time, and ensure compliance.
a. Inventory Management Software
At the core of every automation system is the inventory management platform. It tracks stock levels in real-time, integrates with POS and EHR systems, and predicts future demand based on historical usage patterns. This forecasting reduces stockouts and waste, especially for high-cost or short-shelf-life medications.
Many systems offer automated vendor reordering, ensuring timely restocks without manual intervention. The software also sets alerts for expiry tracking, batch recalls, and controlled substance audits, making compliance more manageable and transparent.
Companies like AppsRhino can build Inventory Management platforms that integrate POS, EHR, and auto-reorder functionality in a single dashboard, reducing the need for multiple disconnected systems.
b. Automated Storage & Retrieval Systems
Once medications are stocked, automated systems handle their storage and retrieval. Using barcode or RFID tracking, these systems log every medication’s exact location. This improves traceability, speeds up picking, and reduces human error.
High-value or sensitive medications like narcotics and biologics are stored with secure access control and temperature-regulated zones. Access logs ensure only authorized personnel handle critical inventory — a vital step in both hospital and retail settings.
c. Robotic Dispensing Units
Robotic arms bring speed and precision to the dispensing process. They scan, sort, and fill prescriptions with minimal human touch. Dual-arm systems can operate simultaneously to boost throughput, while camera-based pill verification ensures the right medication and dosage are selected every time.
These units are also compatible with both blister packs and vial-based packaging, making them flexible for different pharmacy formats.
d. Labeling & Packaging Units
After dispensing, automation takes over labeling and packaging. These units print FDA-compliant labels that include drug name, strength, dosage, and usage instructions. Tamper-evident seals are applied for safety, and personalized dosing labels can be printed for individual patients, especially useful in nursing homes and chronic care setups.
Some advanced systems even include photo verification, capturing images of each dispensed item to support audit trails and remote pharmacist checks.
Pharmacy automation systems don’t work in silos. When each component — software or hardware — is connected through a unified platform, pharmacies gain complete visibility across their workflow. From inventory to the patient’s hand, every step becomes traceable, safer, and faster.
Types of Pharmacy Automation (By Functional Stage)
Pharmacy automation systems include several functional areas, from storage to reporting, each powered by specialized systems to enhance accuracy and efficiency.
1. Storage & Dispensing Automation
These systems manage medication inventory and ensure accurate, efficient dispensing with minimal human touch.
- Automated storage cabinets with barcode/RFID tracking
- Robotic dispensing arms for high-volume prescription filling
- Secure access control for narcotics and high-risk drugs
- Real-time inventory updates to prevent stockouts
- Integration with EHR and POS systems
2. Compounding Automation
Used in hospital pharmacies and sterile environments to mix IV bags, chemo doses, or personalized drugs under safe conditions.
- Automated IV compounding robots
- Closed-system transfer devices (CSTDs) for cytotoxic drugs
- Gravimetric verification to ensure correct dosing
- Laminar flow hoods with integrated weighing scales
- Operator prompts and touchscreen recipes
3. Packaging & Labeling Automation
These systems prepare medications for final delivery with accurate, compliant packaging and patient-specific labeling.
- Blister pack and vial packaging units
- Label printers compliant with FDA standards
- Tamper-evident seal application
- Personalized dosage labels (per patient or shift)
- Barcoded unit-dose packaging
4. Data Management Automation
Software platforms that store, organize, and manage prescription, inventory, and patient data securely across workflows.
- Centralized database for all prescription records
- Integration with EHR, LIS, and pharmacy benefit managers (PBMs)
- Access control and user logging
- Cloud-based dashboards for remote visibility
- Backup and disaster recovery systems
5. Analytics & Reporting Automation
Extracts and visualizes key insights from pharmacy operations to improve decisions and regulatory compliance.
- Real-time performance dashboards
- Drug usage trend forecasting
- Expiry, wastage, and inventory turnover analysis
- Regulatory compliance and audit readiness reports
- AI/ML models for anomaly detection or refill prediction
Pharmacy Automation System Workflow: Step-by-Step Operations
Understanding how pharmacy automation systems operate in real time helps clarify their true value. Here’s a step-by-step walkthrough of a typical automated workflow, showing how software and hardware work together alongside pharmacy staff to manage both new prescriptions and refills.
1. Prescription Submission
Prescriptions arrive via various sources:
- EHR integration from hospitals or clinics
- e-Prescriptions from physicians
- Scanned uploads or manual entries at the pharmacy counter
Once received, the system logs the prescription and matches it against the patient profile, checking for allergies, dosage conflicts, and interactions.
2. Stock Verification & System Trigger
The automation software instantly checks real-time inventory. If the medication is available, it reserves stock for the prescription. If it’s a refill, the system may already have pre-filled queue logic to prioritize processing.
If stock is low or unavailable, the system flags it for either manual override or automatic vendor reordering, depending on the configured rules.
3. Pharmacist Review & Approval
Before any dispensing begins, a licensed pharmacist reviews the prescription digitally.
Key checks include:
- Correct medication and dosage
- Patient history and potential red flags
- Manual overrides or adjustments if needed
Once approved, the system moves forward with automated execution.
4. Automated Picking & Dispensing
Now the hardware takes over:
- Storage and retrieval systems locate the medication
- Robotic dispensers pick the required quantity.
- Camera systems verify pills or vials against the prescription.
- Redundant checks catch misfills before they proceed.
This stage significantly reduces human error and handles multiple prescriptions simultaneously, improving throughput.
5. Labeling, Packaging & Photo Verification
Next, the medication moves to the packaging unit. Here, it’s:
- Labeled with FDA-compliant information
- Marked with patient-specific dosing instructions
- Sealed with tamper-evident packaging
Some pharmacy automation systems also perform photo verification, capturing an image of the labeled medication for final pharmacist review or audit compliance.
6. Staff Verification or Final Review
A pharmacy technician or pharmacist performs the last check, often using digital dashboards that show:
- Patient name
- Medication image
- Dosage instructions
- Time stamps of each process stage
For sensitive medications, biometric or password verification may be required before release.
7. Notification & Pickup or Delivery
Once verified, the pharmacy automation system automatically notifies the patient:
- SMS alerts or in-app notifications inform them that their prescription is ready
- Options for pickup scheduling or delivery tracking are made available.
- Refill reminders are scheduled within the system
For hospital settings, medication is routed directly to wards or patient rooms via delivery carts or pneumatic tubes.
This integrated workflow shows how pharmacy automation systems enhance safety, speed, and transparency. Every step is traceable, repeatable, and built for scale, freeing pharmacists to focus more on patient care and less on manual tasks.
Benefits of Pharmacy Automation Systems
Implementing pharmacy automation systems is about unlocking tangible improvements across operations, staff performance, and patient experience. From reducing errors to saving valuable time, here are the key benefits pharmacies are seeing:
Reduced Wait Times
Automated workflows drastically cut down the time needed to fill prescriptions. Tasks that once took several minutes per order, such as sorting, counting, labeling, and verifying, are now completed in seconds.
Increased Staff Productivity and Retention
By automating repetitive and manual tasks, pharmacy teams can shift their focus to clinical consultations, patient education, and quality checks.
This reduces burnout and improves job satisfaction, especially in high-volume retail and hospital pharmacies where staff shortages are common. Technicians can do more meaningful work, and pharmacists have more time for high-value interventions.
Improved Accuracy and Safety
With robotic dispensing, barcode/RFID tracking, and photo verification, the risk of human error drops dramatically. Automation systems offer built-in safety checks, real-time alerts, and dual-verification options to ensure the correct medication reaches the right patient every time.
Regulatory Compliance and Audit Trails
Every transaction in an automated system is logged — from inventory changes and refill activity to access controls and patient-specific data. This generates an auditable trail that helps pharmacies comply with regulations like the FDA, HIPAA, and DEA, especially in controlled substance handling.
Enhanced Patient Satisfaction
Faster service, fewer medication errors, and personalized packaging all contribute to better patient experiences. With SMS or app-based notifications, patients know exactly when and where to collect their prescriptions, reducing uncertainty and increasing trust in the pharmacy.
Pharmacy automation systems aren't just tools — they’re enablers of consistency, compliance, and care. With the proper setup, they quickly pay for themselves in both time and outcomes.
Challenges and Limitations
While pharmacy automation systems offer measurable benefits, adopting them does come with a few hurdles, especially during the early stages of implementation. Addressing these challenges up front can help pharmacy leaders make informed, scalable decisions.
Integration with Legacy Systems
One of the most cited barriers is the complexity of integrating new automation platforms with older EHRs, POS systems, or local databases. Many pharmacies still use fragmented software, and connecting these to modern automation tools often requires custom APIs, middleware, or third-party support, which can extend implementation timelines.
Cybersecurity & Cloud Risks
As pharmacy systems move toward cloud-based operations and IoT devices, cybersecurity becomes a top concern. Data breaches or unauthorized access to prescription data could have legal and reputational consequences. Choosing vendors with HIPAA-compliant architectures, end-to-end encryption, and audit-ready access logs is non-negotiable.
Downtime and Recovery
Automated systems rely on continuous uptime to function smoothly. In the event of a technical failure or power outage, pharmacies must have manual override protocols or recovery workflows in place. Without proper training, such interruptions can stall operations.
Vendor Lock-In and Scalability
Some automation solutions are closed ecosystems, meaning upgrades or component swaps must go through the same vendor, limiting flexibility. Pharmacies should look for modular systems that scale with demand and allow interoperability with other platforms over time.
When planning your automation journey, being aware of these limitations ensures a smoother rollout and longer-term value.
Real-World Use Cases of Pharmacy Automation
Pharmacy automation systems have been successfully implemented in various healthcare environments, demonstrating significant improvements in efficiency, accuracy, and patient satisfaction. Below are three illustrative case studies:
Hospital: University Hospitals Coventry and Warwickshire NHS Trust (UK)
Problem: The hospital faced challenges with medication errors and workflow inefficiencies across multiple sites.(Source: WIRED)
Solution: Integration of Omnicell’s automated dispensing cabinets with the hospital’s Electronic Patient Record (EPR) system, utilizing standard protocols like HL7 and FHIR for seamless communication.
Result: This integration led to a 20% reduction in medication errors and improved workflow efficiency across the trust’s multiple sites. (Source: Omnicell.co.uk)
Retail Chain: Walgreens Micro-Fulfillment Centers (USA)
Problem: High prescription volumes and pharmacist burnout due to repetitive tasks. (Source: Axios)
Solution: Establishment of micro-fulfillment centers equipped with robotic systems capable of filling up to 50,000 prescriptions daily, thereby automating the dispensing process.
Result: This automation allowed pharmacists to focus more on patient care, reducing burnout and improving service delivery.
Nursing Home: Centralized Dosing Automation
Problem: Manual medication administration processes were time-consuming and prone to errors, affecting patient safety (Source: japha.org)
Solution: Implementation of a centralized robotic pill dispensing system that automates the preparation and distribution of medications.
Result: The system improved medication dispensing accuracy, reduced dispensing time, and increased patient safety. (Source: ritetechnologies.net)
These case studies underscore the versatility and effectiveness of pharmacy automation systems in enhancing operational efficiency, reducing errors, and improving patient outcomes across different healthcare settings.
Technologies in Pharmacy Automation Systems
Pharmacy automation systems combine software intelligence and physical automation tools to streamline every aspect of medication management.
Software Technologies
Software manages logic, data, workflows, and communication between systems and users across the pharmacy lifecycle.
- Pharmacy Management Systems (PMS)
- Electronic Health Record (EHR) integrations (HL7/FHIR support)
- Auto-reorder and demand forecasting engines
- Patient-facing apps with notification & refill options
- Data analytics dashboards & reporting tools
- AI/ML models for predictive operations and verification
- Cloud-based platforms with role-based access
Hardware Technologies
Hardware executes physical tasks like storage, dispensing, compounding, and packaging with speed and precision.
- Robotic dispensing units (single or dual-arm)
- Automated storage & retrieval systems (ASRS)
- IV compounding robots with gravimetric checks
- Smart label printers & blister packaging machines
- RFID/barcode scanners and access control panels
- Secure temperature-controlled storage zones
- Integrated touchscreen stations for staff use
Together, these technologies form the foundation of modern pharmacy automation systems, enabling seamless, data-driven, and error-resistant operations across every stage of medication management.
Conclusion
As pharmacies navigate growing demand, limited staff, and rising accuracy standards, pharmacy automation systems have emerged as a critical solution, not just to keep pace, but to lead.
By integrating software intelligence with advanced robotics and secure workflows, automation is transforming how medications are stored, dispensed, and delivered. From hospitals and retail chains to long-term care facilities, the results speak for themselves: faster service, fewer errors, and greater patient satisfaction.
At AppsRhino, we specialize in delivering scalable software solutions that power every stage of the pharmacy automation journey — from inventory management and labeling to real-time analytics, patient notifications, and AI-driven workflows.
Whether you're building a standalone pharmacy platform or modernizing an enterprise operation, our team can help you automate, integrate, and scale with confidence.
👉 Get in touch with us to build your pharmacy automation solution
Frequently Asked Questions (FAQs)
How do I determine which parts of my pharmacy should be automated first?
Start by analyzing where your team spends the most time on repetitive, low-value tasks, such as manual pill counting, inventory checks, or labeling.
Focus on bottlenecks that affect turnaround time or patient safety. Many pharmacies begin with inventory and dispensing automation before expanding to packaging or analytics.
Can pharmacy automation systems be implemented in phases, or do they require full deployment from day one?
Yes, most systems are modular and can be rolled out in phases.
You can start with core components like inventory and dispensing, then scale to packaging, verification, or cloud-based analytics as your needs grow.
This phased approach reduces disruption and spreads out costs.
What kind of training is required for staff to work with automation systems?
Training typically includes basic software navigation, responding to system alerts, and handling exception workflows.
Most vendors offer hands-on training, online modules, and on-site support during rollout. Staff usually adapt quickly, especially when the system reduces repetitive workload.
How do automation systems handle controlled substances or high-risk medications?
These medications are managed using secure storage, biometric access controls, and audit-ready logs.
Systems often apply extra verification steps — like dual sign-offs or photo capture — to ensure compliance with DEA and institutional regulations.
Can automation systems help with multi-location pharmacy networks?
Yes, enterprise-grade pharmacy automation systems can centralize operations across multiple locations.
Features like shared inventory visibility, central data dashboards, and remote management allow chain pharmacies to standardize workflows and reduce redundancy at scale.
Table of Contents
- Key Components of Pharmacy Automation Systems
- Types of Pharmacy Automation (By Functional Stage)
- Pharmacy Automation System Workflow: Step-by-Step Operations
- Benefits of Pharmacy Automation Systems
- Challenges and Limitations
- Real-World Use Cases of Pharmacy Automation
- Technologies in Pharmacy Automation Systems
- Conclusion
- Frequently Asked Questions (FAQs)